Personnel from the School of Electrical and Computer Engineering (ECE) are busy using their knowledge and resources to provide equipment to healthcare workers and develop a novel new testing procedure that could be a game-changer in the fight against COVID-19.
On March 16, 2020, the Georgia Institute of Technology’s Atlanta campus was closed for all non-essential business due to the global coronavirus pandemic. Two weeks later and for the first time in the Institute’s 136-year history, in-person classroom instruction was moved online. Campus is now quiet and sparsely populated, but behind the scenes personnel from the School of Electrical and Computer Engineering (ECE) are busy using their knowledge and resources to provide equipment to healthcare workers and develop a novel new testing procedure that could be a game-changer in the fight against COVID-19.
“The situation has definitely presented challenges to the way we typically do things, but it is also providing a real-life opportunity for us to prove our worth as innovators. Times like these are why we are here, why we do what we do. I couldn’t be prouder of how the ECE community has risen to the current challenge,” said Magnus Egerstedt, Steve W. Chaddick School Chair and Professor in the School of ECE.
One of the most immediate needs that came to the attention of the Institute was the shortage of Personal Protective Equipment (PPE) at Atlanta-area hospitals. The entire campus sprang into action to collect and donate PPE. The Institute for Electronics and Nanotechnology (IEN), directed by ECE faculty member Oliver Brand, donated cleanroom gowns, chemical-resistant gloves, aprons, caps, shoe covers, face shields and masks, safety glasses, and isopropanol to Emory University Hospital. The effort was coordinated by IEN staff members Charlie Turgeon and Dean Sutter and resulted in 55 cases of equipment being donated.
In the Interdisciplinary Design Commons (IDC) makerspace, Kevin Pham, IDC director, and Ian Heaven, a graduate teaching assistant, are using 3D printers to print valves to retrofit a scuba mask and turn it into a Bilevel Positive Airway Pressure (BiPAP) device. The IDC team is also working with Shannon Yee, an associate professor in the George W. Woodruff School of Mechanical Engineering, to fabricate circuit boards for ventilators. A prototype has been tested and production will begin soon.
On the diagnostic side, Manos Tentzeris, Ken Byers Professor in Flexible Electronics, research scientist Yunnan Fang, and graduate students from Tentzeris’ ATHENA research team are working on a cutting-edge means to test for coronavirus that utilizes ink jet technology and antibodies and proteins to create ultra-scalable, safer, quicker, and more accurate testing. This research is funded through Tentzeris’ Ken Byers Professorship. Trials using COVID-19 antibodies supplied by Emory University’s Microbiology Department are currently being conducted. The high-risk approach would typically require 12 to 18 months, but Tentzeris and Fang are working around the clock to bring this method to the public in two to four weeks.
“The next few weeks and months will be a test of our ingenuity, flexibility, and resourcefulness. We must not only be resilient, but audacious. This is an incredibly difficult time for our global community, but I believe the next great set of inventions will be born from these challenges and they will come from the minds and hearts of engineers and scientists,” said Egerstedt.
Additional Images
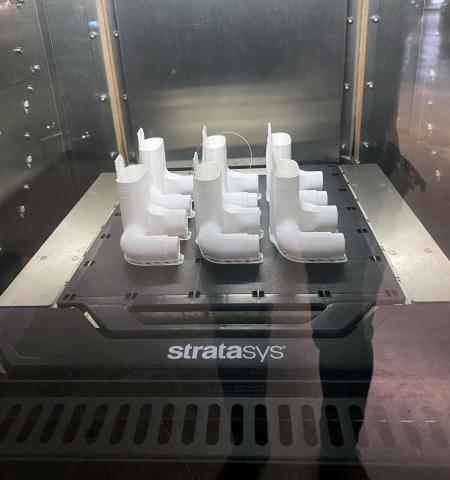